Case Studies
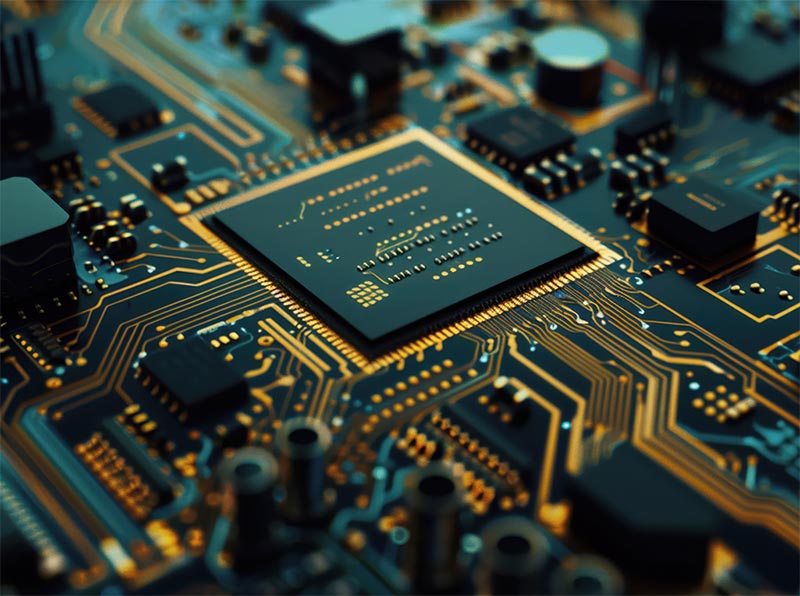
Large Semiconductor Fab in US
Optimizing ultra-high purity electronic gases production through Automatic plant start-up, automatic load changes, and yield optimization

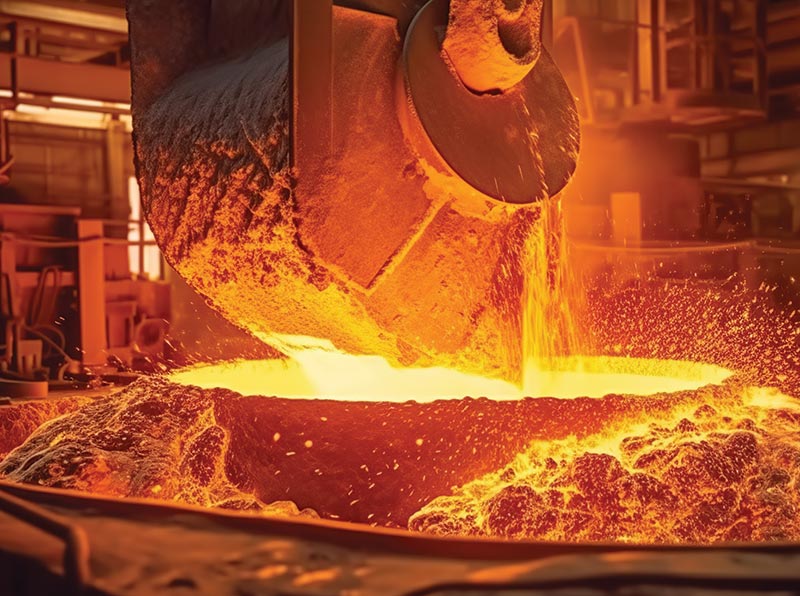
Major steel-works in Germany
Optimizing Oxygen supply and Argon production for constant major demand changes using self-learning AI Plant Control

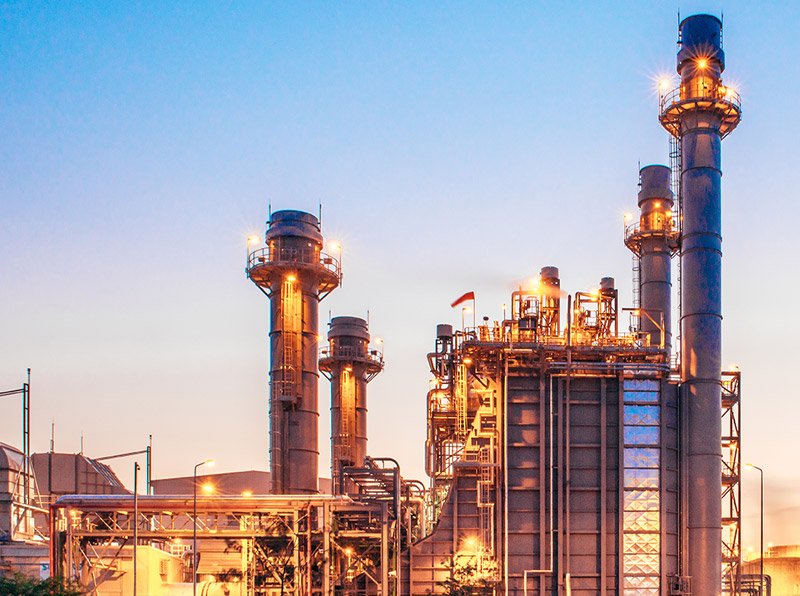
Ethylene Cracker in US
Automating furnace operations with Automatic Sequence Transition. Avoiding coil damage through real-time coil temperature profile monitoring

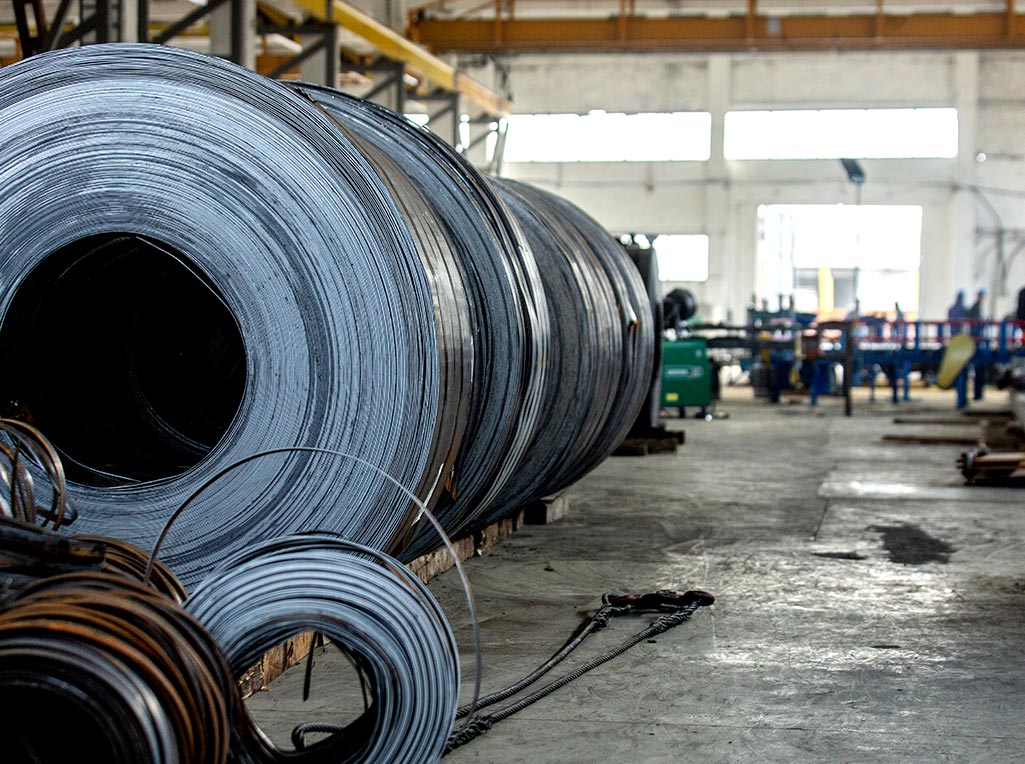
European steel producer
Real-time optimization to address operator’s challenge of complex network operations and plant’s shortcomings of product waste, inefficiencies and reliability risks

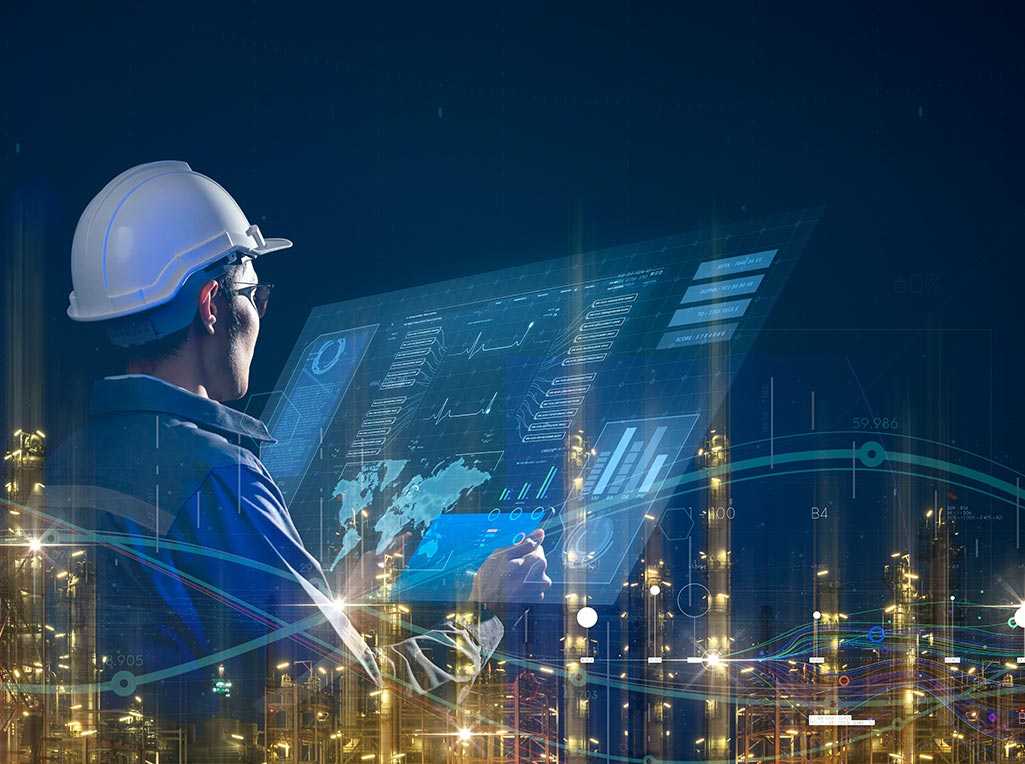
Leading Integrated Petrochemical Manufacturer, Asia
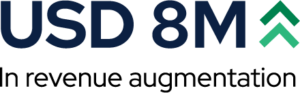
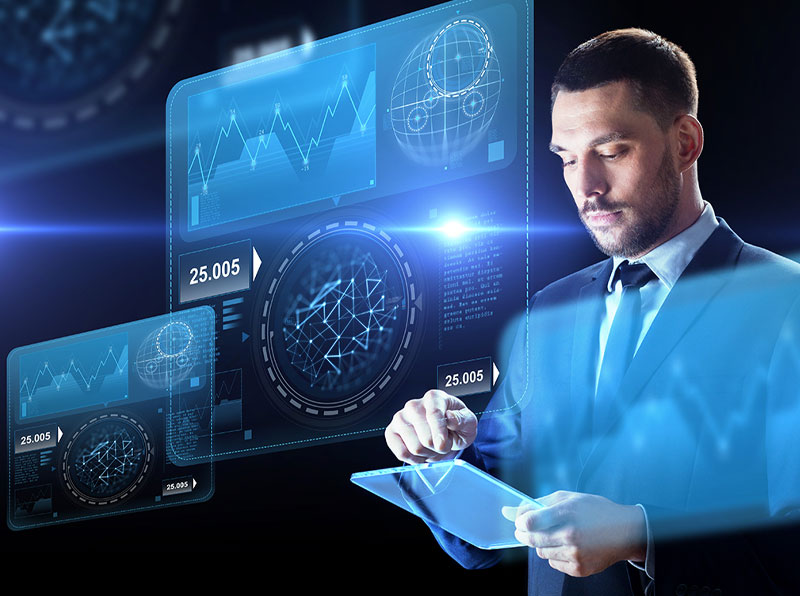
Transforming Plant Reliability with Gen-AI: A Blueprint for Intelligent Operations in Specialty Chemicals
A global specialty chemicals leader deployed Gen-AI powered solution to detect complex, pattern-based anomalies across critical assets. By combining historical data, OEM insights, and financial overlays, the system enabled faster, smarter operator decisions—delivering up to $5M in business impact.

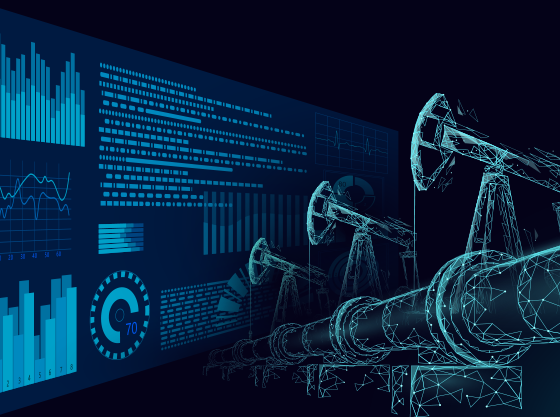
AI-Powered Conversion Optimization for a Leading European Downstream Operator - Enhancing Process Stability and Conversion Efficiency
A leading European refiner deployed an AI – powered solution to optimize LC-FINING operations, improving anomaly detection, feed operability forecasting, and conversion efficiency – delivering up to 2% yield gain, enhanced process stability, and smarter catalyst management through predictive, model-driven decision support.
